Etude de cas : Un boitier de conception métallo-plastique IK8
Dans cet article, nous allons vous partager les étapes clés du développement d’un boitier sur mesure réalisé en partie en plastique et en tolerie fine pour l’un de nos clients.
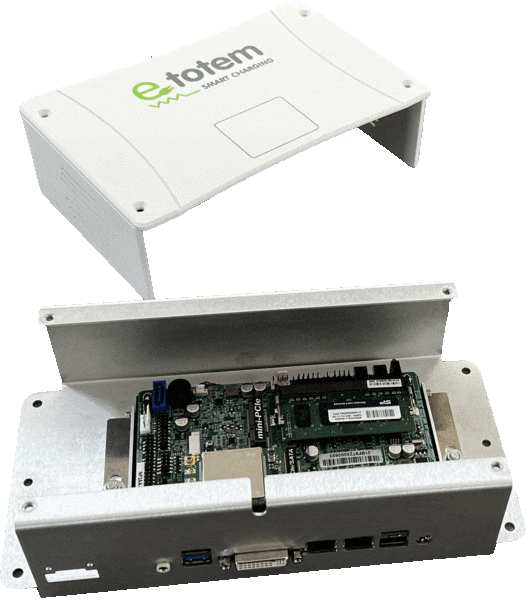
Le produit
Il s’agit d’un produit destiné à etre embarqué dans une borne de charge pour véhicule electrique, il intègre une carte electronique et le respect des normes impose une solution technique offrant le meilleur compromis en terme de solidité, d’esthétique…
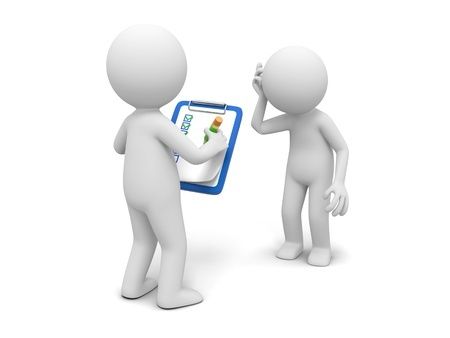
Le besoin du client
Notre client souhaitait développer un boitier permettant de recevoir une carte electronique, 4 critères à respecter :
- Rapport qualité prix optimisé (ratio esthétique, solidité, résistance à la corrosion, simplicité d’accès),
- Prise en charge du développement (étude, réalisation des prototypes, essais IK, intégration electronique)
- Rapidité de mise en œuvre pour un déploiement d’une 1ere série en moins de 3 mois.
- Gérer l’emballage du produit dans un carton unitaire imprimé
- Marché annuel 50 à 100 pièces
La solution proposée
Compte tenu des faibles quantités à produire, le procédé de fabrication de boitiers en plastique sur mesure proposé par ATOPLAST (procédé de tôlerie plastique : solution sans frais de moule et d’outillage) répond parfaitement aux attentes du client et offre également l’avantage d’une souplesse en cas d’évolution du produit.
Par ailleurs, certaines contraintes du CDC nécessitaient une solidité renforcée, et le choix de l’association d’une matière métallique fut évoqué dès le départ. Grace à notre complémentarité avec ATOMELEC nous avons très facilement su concevoir et réaliser un boitier de conception métallo-plastique
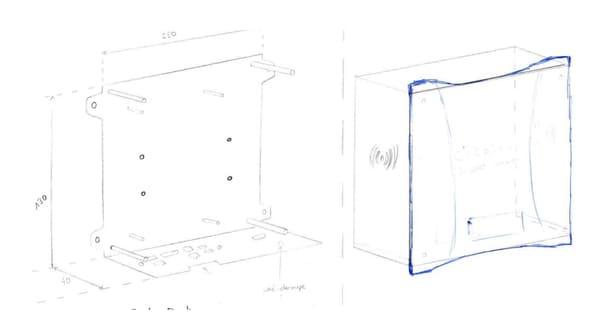
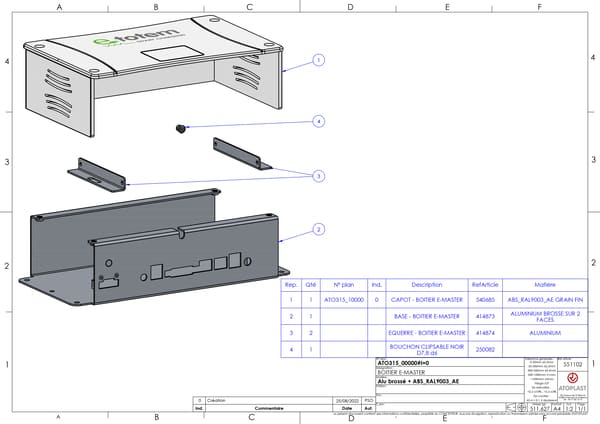
Déroulement de la phase développement
- Septembre 2022 premier contact pour ce projet
- Le client nous sollicite pour lui faire une proposition.
- Données d’entrée : Cahier des charges avec encombrement de la carte electronique, nombres de connectiques, mode de fixation dans la borne, respect d’un IK 8, quantité de boitier à produire, objectif coût…
- Septembre 2022 Etude de faisabilité :
- Fourniture d’un premier croquis de conception avec chiffrage associé
- Suite à remarques du client, modification de la conception et fourniture d’une nouvelle offre de prix
- Octobre 2022 Commande client
- Mise en œuvre de l’étude 3d et fabrication du prototype (pièce identique au modèle de série), contrôle dimensionnel, essais d’intégration
- Novembre 2022 :
- Réalisation des essais IK afin de valider le respect du cahier des charges. Succès pour cette conception qui est validée IK8
- Reflexion sur l’ajout d’une sérigraphie sur la face avant
- Fin novembre 2022 Commande client d’une 1ere série, pour une livraison en décembre 2022, soit 3 mois pour réaliser le développement et la fabrication d’un premier lot de 100 boitiers.
Informations techniques
- Matière ABS UL94V0 RAL 9002, épaisseur 3 et 4 mm et tole en Alu finition brossée
- Finition sérigraphie 1 couleur sur la face avant
- Fourniture et pose des colonnettes pour le maintien de la carte electronique.
- Process atelier :
- Plasturgie : (découpe et usinage de la matière, pliage à chaud, assemblage par soudure à froid, sérigraphie du logo
- Tolerie : Découpe laser, brossage, pliage et sertissage des colonnettes et inserts
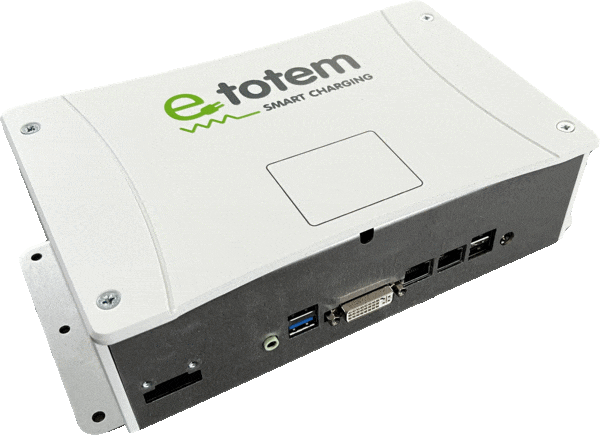
Information tarifaire
- Cout du développement : Etude 3d, essais IK et fabrication du prototype : 1500 €
- Cout en série : 42€ PUHT pour la partie métalloplastique seule par 100 pièces